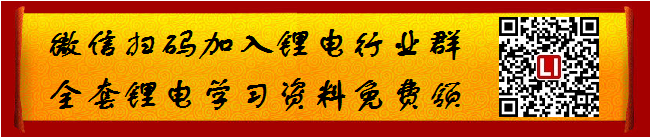
在20世纪,铜作为电极材料在电火花加工中被广泛使用。那时只有在制作大型电极且模具加工要求不高或粗加工时,石墨材料才会成为备选考虑。一些早期接触过石墨电极的技术人员曾有普遍印象:石墨材料脏、易掉渣、表面效果不好、加工效率不高等等。
随着高新技术的发展,石墨材料的制造工艺不断完善,能满足不同电火花加工需求的石墨材料层出不穷,市场上石墨高速铣削机床应运而生,数控电火花加工机床的石墨放电性能也有了全面的提升。当今,在制造技术领先的欧洲,模具企业超过90%的电极材料采用石墨。航空航天、汽车、家电、电子等模具已大范围采用石墨作为电极材料,这种显著变化归功于石墨电极可实现高效率、高品质加工等诸多优势。
但在中国,当前大多数模具企业还是选用铜作为主要的电极材料。根据石墨材料的特性,以下全面分析其电火花加工的优势与不足,介绍如何正确选择石墨材料、电极制作与放电加工的要点,并提供实际应用案例。
2.1 放电加工速度
石墨是一种非金属材料,熔点极高,达3 650℃,而铜的熔点是1083 ℃,因此石墨电极能承受更大的电流设定条件。当放电面积与电极尺寸缩放量越大时,石墨材料高效率粗加工的优越性越显著。石墨的导热系数是铜的1/3,其放电过程中产生的热能可更有效地用于去除金属材料,因此在中、精加工中,其加工效率也比铜电极要高。根据加工经验,在正确的使用条件下,石墨电极的放电加工速度要比铜电极整体快1.5~2倍。
2.2 电极损耗
石墨电极具有能承受大电流条件的特性,另外,在合适的粗加工设定条件下,含碳元素的钢工件在加工时产生的蚀除物和工作液在高温下产生的分解物中的碳颗粒,在极性效应的作用下,部分蚀除物、碳颗粒会粘附在电极表面形成一层保护层,保证了石墨电极在粗加工中的损耗极小,甚至是“零损耗”。电火花加工中主要的电极损耗量来自于粗加工,精加工设定条件虽然损耗率较高,但因零件预留加工余量不多即加工蚀除量较少,其总体损耗量也较少。总体而言,石墨电极在大电流的粗加工中损耗会少于铜电极,在精加工中损耗可能会稍大于铜电极,二者的电极损耗情况相当。
2.3 表面质量
石墨材料的颗粒直径直接影响电火花加工的表面粗糙度,直径越小可获得更低的表面粗糙度值。几年前使用颗粒直径φ5 μm的石墨材料,电火花加工的最佳表面只能达到VDI18(Ra0.8 μm),现今石墨材料的颗粒直径已能达到φ3 μm以内,电火花加工的最佳表面可稳定达到VDI12(Ra0.4 μm)或者更精细的等级,但石墨电极无法进行镜面电火花加工。铜材料的电阻率较低,组织结构致密,电火花精加工易获得稳定的加工状态,在较困难的条件下也能稳定加工,表面粗糙度可小于Ra0.1 μm,能进行镜面电火花加工。
由此可见,如果放电加工追求极其精细的表面,使用铜材料做电极更加合适,这是铜电极较石墨电极的主要优势。但铜电极在大电流设定条件下,电极表面容易变得粗糙不堪,甚至出现裂纹,而石墨材料则没有这方面的问题,对于表面粗糙度要求为VDI26(Ra2.0 μm)左右的型腔加工,使用1个石墨电极即可完成从粗到精的加工过程,实现均匀一致的纹面效果,表面不会有缺陷。另外,由于石墨与铜材组织结构的不同,石墨电极表面放电的腐蚀点比铜电极要规则,因此在加工VDI20及以上相同表面粗糙度时,使用石墨电极加工的工件表面颗粒度更加分明,这种纹面效果要优于铜电极的放电表面效果。
2.4 加工精度
石墨材料的热膨胀系数小,铜材料的热膨胀系数是石墨材料的4倍,因此在放电加工中石墨电极相比铜电极不易发生变形,可获得更稳定可靠的加工精度。尤其是在加工深窄筋位部分时,局部高温容易使铜电极发生弯曲变形,而石墨电极不会这样;对于深径比大的铜电极,在加工设定时还需要补偿一定的热膨胀值来修正尺寸,而石墨电极不需要。
2.5 电极重量
石墨材料较铜的密度要小,相同体积的石墨电极重量仅为铜电极的1/5。可见体积较大的电极使用石墨材料非常合适,极大地减轻了电火花加工机床主轴的载荷,电极不会因为重量大而导致装夹不便、加工中产生偏摆位移等问题,可见在大型模具加工中使用石墨电极很有意义。
2.6 电极制作难度
石墨材料的机械加工性能好,切削阻力仅为铜的1/4,在正确的加工条件下,铣削加工石墨电极的效率是铜电极的2~3倍。石墨电极容易清角,可以将平时要由多个电极完成的工件设计成一个整体电极来加工。石墨材料独特的颗粒组织结构,使得电极铣削成型后不会产生毛刺,对于复杂造型不便于去除毛刺的情况直接满足使用要求,省去了人工对电极进行抛光的工序,避免了抛光导致的形状改变、尺寸误差等。
需要注意的是,由于石墨是粉尘堆积物,铣削石墨时会产生大量的粉尘,因此铣削机床必须要有密封与吸尘装置。如果需要使用电火花线切割加工石墨电极,其加工性能就不如铜材料了,切割速度相比铜慢约40%。
2.7 电极安装与使用
石墨材料的可粘结性好,可以使用导电胶将石墨与夹具粘结的方法铣削电极、放电加工,可省去在电极材料上加工螺丝孔的工序,节省了工作时间。石墨材料比较脆,特别是细小窄长电极,在使用中受到外力作用时容易折断,但可以马上知晓电极发生了损伤。如果是铜电极则只会弯曲不会折断,这种状况在使用过程中非常危险且难以发现,很容易导致工件报废。
2.8 价格
铜材料是不可再生资源,价格趋势会越来越贵,而石墨材料的价格趋于稳定。近几年铜材料价格不断上涨,而各大石墨制造商不断改进制作石墨的工艺使其更具性价比优势,如今,相同体积下,通用性石墨电极材料的价格与铜电极材料的价格相当,但石墨所能实现的高效率加工,比使用铜电极要节省的大量工时,相当于直接地降低了生产成本。
综上所述,在石墨电极的8项电火花加工特性中,其优势明显:铣削电极与放电加工的效率均显著优于铜电极,大电极重量小,尺寸稳定性良好,薄片电极不容易发生变形,表面纹理优于铜。石墨材料的不足之处是不太适合VDI12(Ra0.4 μm)以下的精细表面放电加工,使用电火花线切割制作电极的效率较低。但从实际角度来看,影响石墨材料在国内不能有效推广的一个重要原因是铣削电极需要有专门的石墨加工机,这就对模具企业的加工设备提出了新的要求,一些小型企业可能不具备这个条件。总体而言,石墨电极特性的优势涵盖了电火花加工的绝大多数加工场合,值得推广应用,长期效益可观,其精细表面加工的不足之可以通过使用铜电极来弥补。
3. 电火花加工用石墨电极材料的选择
对于石墨材料,主要有以下4个指标直接决定着材料的使用性能:
1)材料的平均颗粒直径材料的平均颗粒直径直接影响到材料放电的状况。石墨材料的平均颗粒越小,材料的放电越均匀,则放电状况越稳定,表面质量越好,损耗情况越小;平均颗粒越大,在粗加工中能获得更好的去除率,但精加工表面效果较差,电极损耗较大。
2)材料的抗折强度材料的抗折强度是材料强度的直接体现,显示材料内部结构的紧密程度。强度高的材料,其放电的耐损耗性能相对较好,对于精度要求高的电极,尽可能选择强度较好的材料。
3)材料的肖氏硬度石墨的硬度比金属材料要高,在切削时刀具的损耗比切削金属要大些。与此同时,硬度高的石墨材料在放电损耗方面的控制比较优秀。
4)材料的固有电阻率固有电阻率较大的石墨材料,放电速度会比电阻率小的慢。固有电阻率越高,电极损耗就越小,但固有电阻率偏高时,放电的稳定性会受到影响。
目前全球知名的石墨供应商中不同供应商有多种不同牌号的石墨可供选择。通常根据石墨材料的平均颗粒直径来分类,颗粒直径≤φ4 μm的定义为细石墨,颗粒在φ5~φ10 μm定义为中石墨,颗粒在10 μm以上定义为粗石墨。颗粒直径越小材料的价格越贵,可以根据电火花加工要求与成本选择合适的石墨材料。
4. 石墨电极的制作
模具制造中的石墨电极主要用铣削加工的方法制作完成。从加工工艺的角度看,石墨与铜是2种不同的材料,应该掌握它们不同的切削特性。如果使用加工铜电极的工艺来加工石墨电极,必然会出现问题,如薄片经常发生断裂,这就要求采用合适的切削刀具与切削参数。
加工石墨电极比铜电极的刀具磨损要大,就经济性考虑,选用硬质合金刀具是最经济的,选择金刚石涂层刀具(称石墨刀)价格较昂贵,但金刚石涂层刀具使用寿命长,加工精度高,整体经济效益不错。刀具的前角大小也影响其使用寿命,前角0°的刀具会比前角15°的刀具高出多达50%的使用寿命,切削的稳定性也较好,但是斜角越大,加工表面越好,使用15°斜角的刀具能达到最佳的加工表面。加工时的走刀速度可按电极的形状来调整,通常为10m/min,与加工铝或塑料类似,粗加工时刀具可直接在工件上下刀,精加工易发生崩角、碎裂的现象,常采用轻刀快走的方式。
石墨电极在切削加工中会产生大量的粉尘,为避免石墨颗粒吸入机床主轴和丝杠,目前解决方案主要有2种,一种是使用专门的石墨加工机,另一种是将普通的加工中心改装,配置专门的吸尘装置。市场上专门的石墨高速铣削机床铣削效率高,可轻松完成复杂电极的制造,电极精度高,表面质量佳。
如果需要使用电火花线切割来制作石墨电极,推荐使用颗粒直径更小的细石墨材料。石墨材料的电火花线切割加工性能较差,其颗粒直径越小时可获得相对较高的切割效率,避免出现频繁断丝、表面条纹等异常问题。
5. 石墨电极的电火花加工参数
石墨与铜材料的电火花加工参数选用有较大差异。电火花加工参数主要包括电流、脉冲宽度、脉冲间隙、极性。以下介绍合理使用这些主要参数的依据。
石墨电极的电流密度一般为10~12 A/cm2,比铜电极要大得多,因此在对应面积允许的电流大小范围内,电流选用越大,则石墨放电加工速度越快,电极损耗越小,但表面粗糙度会变粗。
脉冲宽度选用越大,电极损耗会降低。但较大的脉冲宽度会使加工稳定性变差,同时使加工速度变慢,表面变粗糙。粗加工时为保证电极低损耗,通常使用较大的脉冲宽度,其取值在100~300 us时可有效实现石墨电极的低损耗加工。精加工时,为获得精细表面与稳定的放电效果,宜选用较小的脉冲宽度。一般石墨电极比铜电极加工时选取的脉冲宽度要减少约40%
脉冲间隙主要影响放电加工速度和加工稳定性,其值越大加工稳定性越好,对获得较好的表面均匀性有帮助,但加工速度会降低。在保证加工稳定的情况下,选用较小的脉冲间隙可获得较高的加工效率,但放电状态不稳定时,脉冲间隙选取较大些可获得更高的加工效率。石墨电极放电加工中通常将脉冲间隙与脉宽宽度按1:1来设定,而通常铜电极加工中脉冲间隙与脉宽宽度按1:3来设定。在石墨加工稳定的情况下,可以将脉冲间隙与脉宽宽度的搭配比例调整到2:3。脉冲间隙较小的情况下,有利于在电极表面形成覆盖层,对降低电极损耗有一定的帮助。
石墨电极电火花加工中极性的选用与铜电极基本相同。根据电火花加工的极性效应,在加工模具钢时通常选用正极性加工,也就是电极接电源的正极,工件接电源的负极。使用较大电流和脉冲宽度,选择正极性加工可以获得极低的电极损耗效果,如果将极性选错将会导致电极损耗变得非常大。只有在表面要求小于VDI18(Ra0.8μm)的精细加工,采用极小的脉冲宽度,才选用负极性加工以获得较好的表面质量,但电极损耗较大。
现在的数控电火花加工机床都配有石墨放电加工参数。电参数的使用是智能化的,可以通过机床的专家系统来自动生成。通常是在编程时选择材料对、应用类型、表面粗糙度值,输入加工面积、加工深度、电极尺寸缩放量等,机床就能配置出优化的加工参数。机床针对石墨电极的放电加工设有丰富的加工参数库,材料类型里可选择粗石墨、中石墨、细石墨对应多种工件材料,将应用类型细分为标准、深槽、尖点、大面积、大型腔、微细等,还提供了低损耗、标准、高效率等多种加工优先权选择。
6. 石墨电极加工应用案例
下图所示手机模具零件的材料S136钢料,加工形状包含形状复杂的加强筋。使用石墨电极,精加工电极使用TTK-4石墨,电极数量2个,粗加工电极尺寸缩放量单边0.08 mm,精加工电极尺寸缩放量单边0.08 mm。粗加工时间3H,精加工时间53 min,表面粗糙度VDI18(Ra 0.8μm)。加工说明:利用石墨的特性将不同形状,将不同高低的众多薄加强筋组合在一个电极上进行放电加工,可减少电极原材料、夹具的投入成本,降低电极的装夹次数和定位工作量,放电时间比使用铜电极加工缩短40%。
7. 结束语
新型石墨电极材料值得大力推广,其优越性将逐渐被国内模具制造行业认识和接受。正确选用石墨电极材料,并配合改进相关工艺环节,将为模具制造企业带来高效率、高品质、低成本效益。
