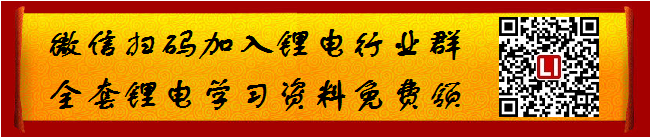
锂电网讯:虽然国内锂电池高端的产品技术指标基本上达到国际先进水平,但产品差距主要体现产品品质管控、产品检测标准的差距上,如何解决这些问题?
动力电池市场,中日韩三足鼎立的世界格局已初步形成,未来电池市场需求增大,行业竞争也异常激烈。
弯道超车,我们真的有那么快吗?
第一宝座,我们还可以坐多久?
在谈到全球新能源汽车的市场情况下,天津巴莫股份有限公司的总经理吴孟涛从三个方面阐述了国内外锂离子动力电池正极材料产业化差距与对策,包括,锂离子动力电池世界格局、国内外正极材料产业差距、企业如何提升国际化。
锂离子动力电池世界格局
中国已经成为全球最大的新能源市场,2016年新能源车的全球销辆是80万台,中国占到40.2万台,达到50%以上。全球现有保有量约200万台,中国同样占有了51%的份额,中国成为了全球最大的新能源车产销市场。
2017年,中国的电动汽车市场份额进一步提升,占整个市场的60%。中国的基数比较大,大概同比增长24%,美国同比增长24%,中国持续成为全球最大的竞争力市场。
可以说整个动力电池世界格局是由巨头车企的选择决定的。
纯电动汽车车企特斯拉选择了松下,奔驰选择了宁德时代,大众和国内的几个厂家有接触,但最后确定的也是宁德时代一家企业,宝马也选择了宁德时代,所以宁德时代是当之无愧的锂电巨头。
还要一些巨头汽车公司选择了日韩电池企业作为汽车供应商,能为国际高端电动车市场供应电池的中国企业仅有CATL等级少厂家,其他的是做一些实验工厂,给奔驰做一些实验工厂,比亚迪是与国际车企巨头有所合作的企业,但不是一级供应商。
国内外正极材料产业差距巨大
动力电池正极材料包括锰酸锂、磷酸铁锂、常规三元材料,高镍材料等新材料的使用需要一步一个台阶,主要是安全性和能量比两方面原因的限制。常规的三元材料和高镍材料,三元材料分单极和多极,国内最优秀的厂家都是用自己的技术,但非常少。
对比国内外主流电动汽车电池体系,中国的北汽原来是磷酸铁锂和三元铁锂,而奇瑞、江淮、上汽、比亚迪,比亚迪原来也是采用的磷酸铁锂。
吉利、启辰晨风,国内的比亚迪电池的容量在慢慢提升。
像3C电池基本上正极材料是一年一更换,而电动汽车要保持一个设计用一段时间,但很难认证,但要进入供应商非常困难。
国际车企像宝马目前用的是523和622,吴孟涛称,“对于宝马使用的动力电池要实现规模化,巴莫需要两年左右的时间。”
企业如何提升国际化
全球动力电池技术向高能量密度、低成本方向发展的技术趋势已经非常明朗,各国政府也先后发布了与此相一致的动力电池发展规划,我国的技术指标要求更高,要求安全性更高、成本更低。
现在国内锂电池行业飞速发展,同时也伴随了尴尬的问题,上游的矿产,原材料价格上涨惊人。
吴孟涛透露,“2015年碳酸锂的价格是3万8一吨,现在最高是18万,目前在17万,还在高位上,暴涨了好几倍。
在设备终端压价严重,行业的规范、产业规范尚不完善,市场有不良竞争,同质化竞争甚至是抄袭现象严重。
产业价值链方面利润的分配是两极化,产业链的核心环节的利润内外受压,不断削薄。
可以说,国内的动力电池企业,除了比亚迪、CATL这两家稍好一些,其他家都非常危险。
在目前情况下,出现了面粉比面包贵的价格倒管现象时有发生,重视技术创新的先进企业难以收回研发成本,盈利非常困难。
吴孟涛说,“我们动力电池的市场显著矛盾是产能不断扩张,高端产品产能严重不足,特别是新型材料。市场的迅猛增长,但是先进企业利润不断下滑。”
第二个方面,国内外正极材料产业差距巨大,国际前10大正极材料厂家占据了国际市场80%以上的市场份额。
现在国际汽车市场收益非常差,包括丰田,在八年之前甚至到十年之前,像大众汽车,把中国知名一点的,包括日韩企业的正极材料都去谈价格,现在手伸得非常长,甚至宝马都到中国去寻找矿资源,到了很多产业链节点,到上游更加延伸。
中国企业把原材料控制以后,全世界都要看中国的眼色,包括美国政府、日本。
像日亚化学、住友金属、三星、当升、湖南杉杉、北大先行都有一些产品。
日亚化学偏重于日本,Umicore的主要客户是LG,LGC也是LG。三星是SDI,当升是LG、SK,日本和韩国核心的电池肯定不会到中国,中国只能做边缘式的,有非常大的竞争力,有专利、知识产权。
吴孟涛说,他们和三星和他一个高管谈,他们认为动力电池中国要落后很多年,材料至少要落后三年以上。
国内锂电池高端的产品技术指标基本上达到国际先进水平,但产品差距主要体现产品品质管控、产品检测标准的差距上,例如磁性异物指标在2010年尚没有被中国企业关注,而国外企业已经要求到ppb的水平。
生产环境Cu、Ze要求在2013年前尚没有被中国企业关注,而国外企业已经完全禁用,国外企业要求该产品指标,且对其检测方法保密,巴莫公司起草了国内第一个磁性异物检测标准及方法,被材料企业和电池企业广泛采用。
国内正极材料差距分析--研发时间的差距。日本从1991年索尼公司研发锂电池,后来是磷酸钴锂、三元材料,锰酸锂。而美国早在1979年即开始技术方面的创新。
对比中美日三国,在动力电池领域,日本是制造强国,美国是创新强国,中国是市场大国。
吴孟涛透露,“特别是专利方面,近期我们正极材料整个行业大的企业很受困扰,交专利费五千万,每年按销售额返还,不然的话国际上肯定惹麻烦。国内的企业都签协议了,今后我们行业协会一定要团结一心,不然的话价格就转嫁到我们锂电池整个行业里面。”
从2013年以后,国内三元材料的专利申请量趋少,在国际上也是这个趋势。以前三元材料的专利申请非常之多。
国内产业化生产线的差距,国外是全密闭自动生产线,信息化数据采集,设备精度高,普遍采用了满足汽车行业的精益生产管理,生产环境控制水平严苛。
国内自动化程度已经大幅改善,但信息化数据采集尚未普及,还有一些半手工的生产线。设备精度不能满足动力电池需求,生产环境控制水平较差。
国内外正极材料的品质管控方面,国内要求达到关键工序CPK1.0,国外达到1.33,关键工序PPK我们达到1.1,国外是1.67,产率国内是95%,国外是99%。检测平台国内是常规粉体检测,国外是微观检测、衡量检测等。
面临国际化竞争的白热化,如何做大我国的产业。吴孟涛提出了一些建议:
一、加快产业升级,智能制造是必然趋势,加强四个优化:
工艺参数优化:加大工艺研发、工程化研发力度,提质增效,优化工艺成本。
设备参数优化:开展高精制制造设备国产化开发。
生产管控升级:逐渐从自动化、信息化到智能化升级,提高生产线预警能力、柔性切换能力,实现产品定制化服务。
检测管控升级:对标国际企业标准,健全检测方法,质量闭环,提高成品。
生产环境升级:温度洁净度控制,车间气压,风淋门、人员控制等等。
二、加强产业合作:产学研合作开发紧密度,形成我国锂电池产业创新能力、产业化能力、产品应用能力的合力,促进产业链的全面、整体提升。这是呼吁中科院等大型院一定要做原创性的,动力电池还是有些波折的,原创性缺失。
三、寻找自身优势,细分市场,差异化开发,打造核心品牌和拳头产品。
四、建立稳定的原材料供应链,降低成本、提升我们的价值,为中国新能源产业作出贡献。通过自有或合作的方式整合上下游产业,取得主要的战略资源优势。原材料核心技术、材料开发核心技术、材料应用核心技术、关键设备核心技术。
五、共同维护良性产业生态,政府支持行业规范,希望政府加大对产业发展起决定作用的核心环节的政策支持,鼓励企业参加国际竞争。
例如我国高镍材料产品性能已经能够与国际水平比肩,尚未能有出口退税政策。如果国内没有良好的带头的话,对国内其他产业也是伤害。
六、鼓励和支持企业进行制备技术和加工工艺的升级改造,着力提升产品的批次稳定性和成品率,从而有效降低锂电产品的生产成本。
尽管面临着困难,锂电行业的未来仍然充满机会,应用市场的利好驱动、政府的合力引导,未来五年将是我国锂电池产业步入由大变强的关键时期。
