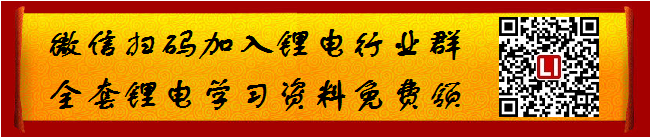
创办于2003年的美国Tesla汽车公司最近又“火”了。2016年8月16日,特斯拉ModelS90D车辆在法国西南部城市比亚里茨(Biarritz)路试时发生起火,车辆尽毁,所幸并无人员伤亡,并且在事故前,车辆就发出了警报,足见Tesla在电动汽车安全方面的工作做得还是非常到位。尽管如此,自上市以来Tesla还是经历了种种“取经磨难”,这里小编先为大家梳理出Tesla的主要安全事故:
世界上没有绝对安全的电池,只有没有充分识别和预防的风险。充份运用以人为本的产品安全开发理念,预防措施虽然不够充分,但安全风险尚可控制。
以2013年ModelS在西雅图高速路上的事故为例,电池包内电池模组之间都有相对独立的空间并由防火结构进行隔离,当车辆底部的电池保护罩被硬物刺穿(冲击力达到25t,并将厚度约6.35mm的车底护板击穿形成直径76.2mm的孔洞)时,造成电池模组发生热失控而起火,但火势并没有迅速蔓延至整个电池包;同时,其三级管理系统也能及时启动安全机制,警告驾驶员尽快离开车辆,最终,驾驶员免于受伤。
Tesla电动汽车究竟运用了何种安全设计,其详情不得而知,因此,我们查询了Tesla电动汽车有关电能存储系统的相关专利,并结合目前可获得的技术信息,图管中窥豹,期望“他山之石,可以为错;他山之石,可以攻玉”,希望能以其失误为鉴,避免重蹈覆辙,同时也能充分发挥山寨之精神,实现吸收再创新。
Tesla Roadster电池包
Roadster是Tesla于2008年量产的首款纯电动跑车,全球限量2500台。该车型搭载的电池包位于座椅后面的行李箱中(如图1所示),整个电池包的重量约450kg,体积约300L,可用能量53kWh,总电压366V。
图1 Tesla Roadster的电池包在车辆内安装位置(左)和实物图(右)
Tesla Roadster电池包由11个模组串联构成(如图2所示);在模组内部,先由69节单体电芯并联构成一个Brick(或称之为“电池砖”),再由9个Brick串联构成一个模组,整个电池包中共有6831节单体电芯。模组是可更换的单元,如果某节电池出问题需要更换,
图2 Tesla Roadster的电池包示意图(左)和装配实物图(右)
可以将包含这节电池的模组进行更换;同时各自独立的模组也能将单体电芯以模组为单元进行分隔。目前,其单体电芯主要选用日本Sanyo生产的18650型锂离子电池。
电动汽车储能系统有关单体电芯容量选型的“大”“小”之争,按中科院陈立泉院士的话说就是电动汽车发展路线之争。目前,由于电池管理技术的限制等多种因素,国内电动汽车的储能系统多采用大容量方形电池,而与Tesla类似采用小容量单体电芯组装电动汽车储能系统的并不多,其中就包括杭州赛恩斯。该公司来自哈尔滨理工的李革臣教授提出了一个新名词“本征安全性”,在电池行业内获得了部分专家认同,即满足两个条件:一是最小容量电芯,其能量限制为单独使用或存放时若发生燃烧或爆炸不足以产生严重后果;二是在电池模块中,一个最小容量电芯若发生燃烧或爆炸,不会引起其他电芯连锁燃烧或爆炸。考虑到当前锂离子电池的安全性水平,杭州赛恩斯也采用小容量圆柱形锂离子电芯,并采用模块化并联和串联连接方式装配电池组(可参考CN 101369649),其电池连接装置及组装示意图如图3所示。
图3 杭州赛恩斯电池串并联连接装置和组装示意图
Tesla ModelS电池包
图 4 Tesla Roadster的电池包在车辆内安装位置(左)和实物图(右)
Tesla于2012年量产的ModelS电池包与Roadster明显不同,其电池包位于车辆底盘下方(如图4所示),并被金属铝板覆盖,总体为平板型布局。参考美国专利US8286743 B2 可知:
Model S电池包(如图5所示)在内部被隔离板划分为7个区域(图5中P1-P7区域),每个区域安装有两个电池模组,每个模组内有370节单体电芯。
在电池包头部还有一个突出部分(图5中P8区域,对应于图4右图所示突起部分),安装了两个电池模组,堆叠排放,电池包内共有5920节单体电芯。
电池包内8个区域(包括突出部分)相互之间是完全隔绝的,一是通过隔离板增加了电池包整体的结构强度,使整个电池包结构更加坚挺;二是当某个区域的电池起火时能有效阻隔,避免引燃其他区域的电池。隔离板内部可以被填充高熔点、低热导的材料(例如玻璃纤维)或水。
电池模组(如图6所示)其内部被“S”型隔离板划分为7个区域(图6中M1-M7区域),“S”型隔离板内部为电池模组的冷却通道,并与电池包的热管理系统相连接。
与Roadster电池包相比较,虽然Model S电池包在外形上有较大变化,但通过独立分区以实现阻断热失控发生蔓延的结构设计仍得到延续。
与Roadster电池包中的单体电芯在车辆内部均平躺排布不同,Model S电池包中的单体电芯均竖立排布。由于单体电芯在发生碰撞挤压而受到外力作用时,沿卷芯轴向受力比径向方向上受力更容易因内部短路而发生热失控,因而从理论上讲,Roadster电池包在侧面遭受碰撞挤压时比在其他方向受力更容易发生热失控,而Model S电池包在底面遭受碰撞挤压时,则更容易发生热失控。
图5Tesla Model S电池包的内部结构示意图
图6 Tesla Model S电池包内的模组示意图
三级电池管理系统
与大部分追求更先进电池技术的厂商不太一样,Tesla没有选用容量更大的方形电池,而是采用了较为成熟的18650型锂离子电池,正是因为Tesla研发的三级电池管理系统。通过采取分层管理的设计,可以同时对数千节电池进行管理,其电池管理系统框架如图7所示。以Tesla Roadster三级电池管理系统为例:
1)在模组的层面上,均设置有BMB (Battery Monitor board) ,监控模组内的每Brick(作为最小管理单元)中各个单体电芯的电压、各Brick的温度以及整个模组的输出电压;
2)在电池包的层面上,设置有BSM (BatterySystem Monitor), 监控整个电池包的运行状态,包括电池包的电流,电压,温度,湿度,方位,烟雾等;
3)在整车层面,设置有VSM (Vehicle System Monitor),用以监控BSM。
另外,在美国专利US20130179012、US 20120105015、US20130049971 A1分别体现了过电流保护、过电压保护、绝缘阻抗监控等技术。
图 7 Tesla Roadster三级电池管理系统架构示意图
