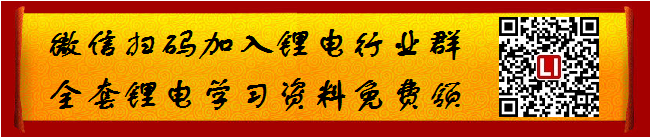
政策调整后,新能源汽车行业正从蛰伏预热逐渐走向爆发,相应的电池行业也将从大规模制造转向优质制造,朝高标准,高安全性,高一致性方向发展。
事实上,动力电池制造产线趋向自动化、智能化、数字化,已经成为业内共识。电池制造企业未来对于MES的需求也将会以高速增长的态势发展。
为致力全产业链更好地协作,从材料、设备、技术等方面推动动力电池行业发展,7月28日-29日,锂电网主办、苏达汇诚协办的“第十届锂电网产业高峰论坛”将在江苏江阴市举行,此次论坛主题为“电动车速抢跑道锂电池渐分高低”,由江阴市人民政府支持。
上海筑思智能科技有限公司总经理邹竹将在本次会议上做“没有MES系统,就没有电池智能制造”的演讲,与业内人士共同探讨MES系统如何实现电池智能制造。
邹竹长期从事动力电池MES应用技术研究和项目实施,于2016年创立上海筑思智能科技有限公司,注力于动力电池领域优质制造,以实现动力电池数字化生产以及可追溯可量化的制造品质为奋斗目标。
实事求是的说,目前国内锂电行业离智能制造还存在较远的距离。一方面国内外锂电设备数字化能力比较欠缺,信息收集不起来;另一方面整个行业都缺乏标准及接口,缺少实现智能制造的所有重要条件。
因此,借助制造执行系统(MES)来实现实时质量监控、工艺着重参数监控、产量及质量的实时查询、生产过程的可追溯性、无纸化生产管理,是实现动力电池智能制造的必然条件。
锂电网了解到,尽管电池智能制造成为一种趋势,行业内对于MES的投资也已经形成了共识,但更多的是雷声大雨点小,特别是在产线投资中,能提前规划MES,并与产线同步实施MES的企业更少。对此,邹竹的回应是:“没有MES系统,就没有电池智能制造”。
所谓智能制造,是基于物联网、大数据、云计算等新一代信息技术,贯穿于设计、生产、管理、服务等制造活动的各个环节,具有信息深度自感知、智慧优化自决策、精确控制自执行等功能的先进制造过程、系统与模式的总称。
在邹竹看来,智能制造是规划出来的,通过MES来实现智能制造的实施和落地可分为三个阶段。
第一阶段:实现全工程数据采集与链接,以品质追溯和设备管理为核心、生产管理为纽带、实现设备互联和数据统一。
第二阶段:提升生产数据分析能力,以品质分析和成本管控为核心,实现生产的精益化管理。
第三阶段:构建基于数据的决策流程,以生产运营效益产出为核心,提升企业生产投资的科学决策。
MES系统对于生产管理最大的核心价值是驱动企业固话工作流程并能持续优化,同时实时监控和规范作业行为,并能对不正确作业方式进行监控。
而如何让企业落实MES系统,邹竹总结了一个成功的等式:
企业MES系统的成功应用=企业清晰的目标规划+可持续发展的软件开发平台+高效的数据采集+良好的项目实施和管理能力
此外,邹竹还指出,企业需要重视新一代生产物流网建设。智能制造的核心课题之一是基础设施建设的弱化,由于在生产物联网缺乏统一规划,统一标准,造成生产现场数据获取困难,为智能制造的快速实施造成了底层壁垒。对此,企业需要从现场设备控制器、通讯协议以及企业数据三个方向建立强制性规范性标准,为后续智能制造的快速实施奠定坚实基础。
值得关注的是,“2017锂电网供应链好产品全国巡回调研活动闭幕式”也将同期举行,经历为期两个月的走访,对超过60家动力电池企业调研之后,高工产业研究院将对外发布巡回调研报告。欢迎业界人士关注“锂电网”网站或微信报名参与。
锂电池产业链企业推广,锂电网(li-b.cn)欢迎投稿。
