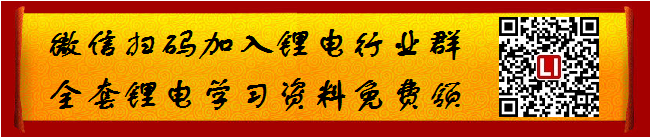
锂电网讯:锂离子电池是一个复杂的体系,包含了正极、负极、隔膜、电解液、集流体和粘结剂、导电剂等,涉及的反应包括正负极的电化学反应、锂离子传导和电子传导,以及热量的扩散等,锂离子电池的电性能、安全性受到多种因素的影响,因此锂电池的设计和生产环节复杂性可想而知,今天小编就带各位读者朋友了解一下从动力电池从“材料选择”到最终产生“电池组”的整个设计和生产流程。
一般而言,锂离子电池的开发分为几个周期,首先是实验室内的基础研究,这一部分主要是适用扣式半电池,或者简单的软包电池,这一步主要的目的是测试材料和配方的性能,因为电池的结构没有进行优化,因此这里得到的结果并不能直接应用在生产上。在进行了实验室级别的初步测试和评估后,好的材料和配方就会转移到下一个阶段——中试阶段,在这一阶段需要考虑电池的综合性能,例如电池能量密度(正负极的涂布量)和快充、倍率等特性,并发现在大规模生产过程中可能面临的工艺问题,及时做出调整。通过上述的过程,完善了电池配方和生产工艺后,成熟的产品才能最终投入正式生产。由于影响锂离子电池性能的因素众多,因此设计和生产或接的每一个参数都会对电池最终的电性能和安全性产生重大的影响,因此我们有必要深入了解材料、设计和工艺参数对于产品最终性能的影响。
1. 电池材料
一款电池的设计要首先从材料的选择开始,需要根据目标需求,例如能量密度、倍率特性、循环寿命和安全等指标,选择合适的材料。正极材料选择方面,我们可以选择橄榄石结构的LiFePO4,这种材料更加适合应用在对能量密度需求不高的大巴车上,此外还有高容量的层状材料,例如NCM和NCA,这些材料由于成本较高,更加适合应用在纯电动汽车上,尖晶石结构的LiMn2O4则更加适合应用在混合动力汽车上。负极材料方面,目前主流的选择是人造石墨、天然石墨和中间相结构碳微球类的材料,在目前动力电池比能力指标不断提高的情况下,我们也会在是石墨材料中添加少量的Si材料(一般<5%),以便提高负极的比容量。为了改善正负极的导电性,通常还需要在其中添加少量的导电剂,目前最常见的导电剂为炭黑类材料,碳纤维类材料,以及近几年兴起的碳纳米管和石墨烯类材料。
此外,为了将活性物质颗粒粘附在集流体的表面还需要添加1-4%的粘结剂,目前的粘结剂主要分为两大类一类是油系粘结剂,主要是PVDF类粘结剂,PVDF具有非常好的电化学稳定性,是目前应用最为广泛的锂离子电池粘结剂之一;另一大类是水系粘结剂,主要为CMC,以及SBR、PAA类的粘结剂。
为了将锂离子电池内的电子传导出来,我们还需要应用到正负极的集流体,主要Al箔和Cu箔,目前主流的铜箔为8um,Al箔为15um,但是随着锂离子电池比能量的不断提高,厂商已经开始采用厚度更薄的6um铜箔和12um的Al箔,但是其强度较差,在使用中容易发生断带和起褶等问题。有时为了降低锂离子电池内阻,提高粘接性,我们还会在铜箔或者铝箔表面涂布一层碳材料(3-5um),例如涂炭Al箔在LiFePO4材料体系中能够起到比较好的效果。
隔膜也是锂离子电池的重要做成部分,它承担着隔绝电子导通离子的作用,目前常见的隔膜制备方法主要分为干法拉伸工艺和湿法工艺,干法拉伸工艺在成本上具有一定的优势,但是干法拉伸工艺制备的隔膜存在明显的各向异性,湿法隔膜在各个方向上的强度基本一致,但是成本较高。目前为了提高锂离子电池的比能量,隔膜的厚度持续变薄,为了保证锂离子电池的安全性,涂层隔膜成为目前隔膜发展的主流趋势,常见的涂层主要可以分为两大类,一类是无机氧化物涂层,例如Al2O3,MgO等,有机物涂层能够显著的提升隔膜的热稳定性;另一类是有机聚合物类涂层隔膜,例如日本厂商采用的比较多的芳纶涂层隔膜,能够有效的提升隔膜的抗氧化性。
电解液也是锂离子电池的重要组成部分,在锂离子电池内部起到传导Li+的作用,目前主流的锂离子电池电解液主要是碳酸酯类电解液(一般至少包含两种以上的碳酸脂类的溶剂,例如EC、DMC、EMC等),Li盐一般采用LiPF6,为了改善电解液在负极表面成膜的质量,我们通常还会在电解液中添加部分的成膜添加剂,例如常见的VC等,在针对硅碳类负极开发的电解液一般还会加入相当数量的FEC,以产生LiF含量 更高的SEI膜,以提高负极SEI的稳定性。此外,为了提高锂离子电池的可靠性和安全性,我们也会在电解液内添加少量的防过充添加剂、阻燃添加剂等成分。
2. 电极生产
在完成了材料的选择后,我们就进入到了下一个环节——电极生产,首先我们要从匀浆开始。锂离子电池的匀浆是锂离子电池生产的关键环节,匀浆环节主要是将活性物质、粘结剂和导电剂等成分混合成为均匀的悬浊液,通常我们会首先将粘结剂分散成为胶液,有一些工艺会将导电剂与胶液分散成为导电胶,然后与活性物质混合,有的工艺会将导电剂和活性物质一起与胶液进行混合,匀浆的关键在于如何将浆料中的各个成分分散均匀,为了达到这一目标需要对匀浆工艺进行优化。目前随着纳米材料的逐渐普及,为了更好的分散纳米级别的材料,锂离子电池厂家也开始采用高速分散设备,利用高速剪切作用,使得浆料分散的更加均匀,此外有也不少材料厂家开发了大量的改善浆料分散行的助剂。
完成了浆料的分散后,下一步就是锂离子电池的涂布了,目前常见的涂布工艺主要有滚涂和喷涂两大类,滚涂设备目前已经逐渐被淘汰,但是滚涂设备好清理,涂布宽度容易调节,仅需要很少的浆料就能够完成涂布,因此在一些中式线和实验室内还有较多的应用。喷涂设备,通过将浆料从喷头处挤压出来转移到集流体上,完成涂布,喷涂设备能够使用粘度和固含量更高的浆料,电极表面状态也更好,因此得到了广泛的应用。在实际生产中涂布速度一般控制在25-50m/min之间,要提高烘干速度主要是通过增加烘箱的长度,这样虽然会增加一部分设备投资,但能够显著的加快生产进度、降低生产成本,但是增加烘箱长度也是有一定极限的,这主要是因为随着烘箱长度的增加会导致集流体张力控制难度的增加,特别是在采用强度较低的超薄集流体时,这一问题也将变得更加突出,因此我们无法无限的增加烘箱的长度。此外高温快速烘干也会加剧PVDF粘结剂在电极内分布不均匀的现象,导致活性物质的粘接力下降,因此我们也很难通过不断提高烘箱温度来提升电极的涂布速度,所以涂布速度的提升是有一定的限制的。
刚刚涂布、烘干后的电极一般孔隙率会在60-70%之间,随后我们会利用辊压机对其进行碾压,使其孔隙率下降到40%左右,这样一方面能够提升电池的比能量,也能够显著的改善电极的导电性和粘结性。辊压机辊轮的直径一般在600-1000mm,较大的辊径能够增加有效碾压区的长度,能够减缓碾压过程中的压力变化速度,这对于厚电极来说尤为重要(厚电极很容易在碾压过程中因为压力过载而引起失效)。
在完成了电极碾压后,我们需要根据电池的结构对电极将电极分切为一定的宽度,然后电极会在真空烘箱中进行干燥,以便出去电极中参与的水分,通常需要将电池中的水分含量控制在500ppm以下,以便将水分对于锂离子电池寿命和副反应的影响控制到最低。
3. 单体电池生产
在电极烘干过程后,我们就进入到了锂离子电池生产的下一个环节——单体电池的生产。为了防止烘干后的电极再次吸收水分,整个单体电池生产环节都需要在干燥间内进行,环境露点一般控制在-40℃到-60℃。方形动力电池电芯的生产工艺主要有三大类,一种是卷绕工艺,这种工艺一般应用在圆柱形电池的生产上,目前也应用在方形电池的生产工艺上,这种工艺的主要优势是生产效率高,可以实现连续生产,缺点也很明显,由于电芯边缘处弯曲角度比较大,因此容易发生电极破碎,产生褶皱,引起缺陷的产生,特别是在厚电极的情况下,这一问题将变的更加严重;第二种是叠片工艺,叠片工艺是一种比较理想的工艺,正负极极片首先会进行冲切,获得特定形状的极片,然后选择正极或者负极极片用隔膜制成封装袋进行保护,然后手工或者叠片机进行叠片,这种工艺的优势是不会引起极片形变,可以采用更厚的电极,但是由于叠片过程是一个非连续的过程,因此叠片工艺的生产效率比较低,采用这种工艺的厂家比较少;第三种是Z型叠片工艺,这种工艺采用连续隔膜,将冲切好的正负极极片放置在隔膜中间,这种工艺在保留了叠片工艺的优势的基础上,也加速了生产过程,提高了生产效率,目前也有比较多的应用。
生产好的电芯首先要焊接极耳,极耳焊接方式主要是采用超声焊接工艺,采用卷绕工艺生产的电芯,受到电芯结构的限制单个电芯无法做的很厚,因此通常会将2-4个电芯并联焊接极耳,组成一个大电芯,叠片工艺生产的电池结构上没有限制,因此一般都是单个电芯焊接极耳。下一步就到了入壳工序,焊接好极耳的电芯外表裹上保护膜后,装入到电池外壳之中,入壳后需要把极耳与电池壳的盖子上的正负极极柱采用超声焊、铆接等工艺连接在一起,然后将电池的上盖和外壳通过激光焊接在一起。
这里我们需要单独谈谈方形电池的上盖,这也是方形电池壳技术含量最高、结构最复杂的地方,这是因为我们不但要保证正、负极极柱之间,以及和电池壳体之间的绝缘,还要保证良好的密封性,避免环境中的水分进入到电池壳体内部,目前最为常见的密封方式为压缩密封,也就是在电极极柱和壳体之间采用塑料件绝缘,并通过压缩塑料件的方式实现电池结构的密封。虽然这一方法简单有效,但是塑料件在长期形变的过程中会发生老化,导致密封可靠性下降,因此也有一些厂家,例如比亚迪开发了Al2O3陶瓷密封工艺,避免了塑料件老化的问题,据称能够保证电池30年以上的密封可靠性,这对于动力电池的梯次利用具有重要的意义。
在完成焊接后,通常还需要进行检漏,并将其中漏率不合格的电池剔除,常见的检漏方法包括直压、倍压和差压等方法,良好的密封性是保证锂离子电池性能长期稳定可靠的关键,因此电池检漏也是方形动力电池生产中必不可少的一个环节。
经过检漏筛选的电池接下来就到了非常重要的注液工序,由于锂离子电池的电解液对水分十分敏感,因此注液过程必须在干燥间内部进行,为了改善电解液的浸润效果,通常需要进行真空注液,也就是首先将电池内部的空气排尽,然后注入电解液,并反复几次,使得电解液在电芯内充分浸润,随后进行封口,并将电池放置在高温环境下以促进电解液的浸润。
电解液充分浸润的电池随后进入到了化成工序,化成主要是通过对电池进行小电流的充放电,对电池进行活化,在首次充电的过程中正极的电势会不断升高,而负极的电势会不断的下降,一般负极电势下降到1V左右时,电解液中的EC组分和其他成膜添加剂,如VC、FEC等就会在负极表面发生分解形成SEI膜,并伴随产气,SEI膜的形成能够阻止负极进一步与电解液发生反应,因此好的SEI膜对于提升锂离子电池的循环性能至关重要,目前通常会通过特殊的成膜添加剂和高温化成等工艺,改善负极SEI膜的质量。此外,由于电解液分解过程中通常会发生产气的问题,产生的气体可能会积累在电芯内,导致电解液浸润不充分,因此有的厂家为了将化成过程中的产气排出,也会将电池封口安排在化成之后。
化成后的电池还需要进行老化,所谓的老化就是将满电态的电池在一定的温度下进行搁置,搁置过程中由于锂离子电池内部的一些副反应,会导致电池的外电压和内阻的变化,通过对电池组的电压、内阻和容量等指标进行监控,能够剔除掉那些自放电不合格和内阻不合格的电池,以提高单体电池的一致性,同时老化结果也是后续的电池组匹配的重要参考依据,为了加速电池老化的速度,提高生产效率,厂家通常会在高温(50-60℃)下进行老化,以缩短电池老化时间。
4. 电池模块和电池组的组装
单体电池完成老化后就进入到模块组合的阶段,在组合之前要首先进行筛选,也就是测试单体电池的容量、动态内阻和电压等数据,尽量选择各个参数一致的电池进行匹配。一个大的电池组通常会由多个电池模块组成,每个电池模块则由多只单体电池通过串联和并联的方式组合而成,串联能够提升电池模块的电压,并联能够提升电池模块的容量,在为电池模块进行单体电池匹配时遵循的原则一般是串联优先考虑容量,避免电池组在充放电过程中容量较低的模块发生过充或者过放。并联则优先考虑内阻,避免在大电流充放电的过程中因为电流分布不均造成的内阻较小的电池发生过充或者过放。
在完成了单体电池的匹配后,就进入到了电池模块的组合工序,这一工序通常是将匹配好的单体电池固定到电池组的模块结构件之中,然后利用汇流排将单体电池的电极极柱连接在一起。虽然电池组中的单体电池都经过了精心的匹配,单体电池的容量和内阻的一致性都非常好,但是在循环的过程由于单体电池衰降速度的不一致,也会导致电池组内单体电池出现电压偏差,为了减少电池组内单体电池不一致性的问题,通常我们还会在电池组内加入均衡器,在电池组内部分单体的电压偏差达到一定程度时,我们会启动均衡器让电池组内的单体电池恢复一致。均衡器按照工作原理一般可以分为耗散型均衡和非耗散型均衡,耗散型均衡结构最简单,就是直接将电池组中电压较高的电池放电,电能转化为热量耗散到环境之中;非耗散型均衡则比较复杂,电压较高的单体电池电量会通过均衡器给电压较低的电池充电,从而实现单体电池之间电压的均衡。
电池组的温度管理也是不容忽视的一部分,温度是影响锂离子电池性能的一个关键因素,特别是在电池组内电池众多的情况下,在充放电发热的影响下,很容易导致电池组内温度分布不均匀,影响电池组的电性能和可靠性,有研究表明电池组内的最大温差从4.62℃,下降到2.5℃就能够将电池组的可靠性从0.0635提高到0.9328(循环200次,无BMS和均衡系统管理),因此电池组内部需要配套良好的加热和散热装置。加热比较简单,通常通过加热带的方式进行升温,近年来也有学者提出了一些电池内部加热的方式快速提升电池温度的方法,散热主要有风冷散热(强制和非强制方式),以及散热效果更好的水冷散热等方式进行。
根据用户的需求,一个动力电池组通常由数个电池模块组成,这些模块通过串联或者并联的方式连接在一起对外供电,满足不同使用场景的需求。
此外,我们还需要为电池组安装管理系统,也就是我们通常所说的BMS,BMS的主要功能是控制电池组的充放电,防止电池发生过充或者过放等问题,此外还需要管理电池组的均衡系统和热管理系统,提升电池组的性能和寿命。为了提升动力电池组的安全性,我们还会在电池组内加入一些热失控预警和阻断装置,以减少电池组热失控造成的危害。
动力电池组从“材料”到“电池组”,普普通通的材料经过锂电人灵巧的双手,经过华丽的转变成为驱动美好新生活的动力来源,可以说每一辆电动汽车、每一颗电芯都凝结着锂电人的心血。
