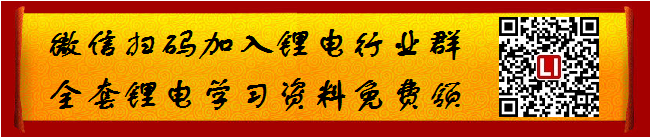
当前,燃料电池处于历史转折期,是从技术开发向商业运作转折的时期。得益于技术进步,燃料电池的性能、寿命、成本三大主要问题正在逐步解决,让商业化发展成为可能。
首先,燃料电池的技术性能基本达到商业运作水平。技术性能的不断提升取决两个前提。一是技术路线的明晰,在研发的起步阶段,出现了各种各样的技术路线,现在多条技术路线基本统一,主流技术已经出现。如高功率的金属板电堆、70MPa的高压氢气瓶,这些都将成为燃料电池汽车的标准配置。
其次,燃料电池的材料、设计以及制造技术趋于成熟。从参考到试验,从加工到生产,我国目前已经掌握了催化剂、膜、炭纸等关键材料的制备工艺,并且批量生产技术趋于成熟。如我国的电解质膜已经成功出口,被应用于几百兆瓦的整机发电设备。
从国际形势来看,燃料电池寿命符合车辆正常使用的要求,可以达到10000小时以上。我国也正在研究通过控制程序和零部件的整合,使燃料电池发动机在整车上的寿命达到5000-10000小时。
值得一提的是,燃料电池寿命的持续提高得益于材料技术的进步。以交换膜为例,如今采用的交换膜强度较10年前有极大的提高,不止强度,催化剂性能也保持稳定,因此燃料电池的耐久性和寿命都有大幅度提高。
技术进步促进燃料电池寿命提高的例子还体现在控制技术方面。经过十几年的努力,我国各大高校和科研机构针对燃料电池的运行条件控制和冷启动保护等项目进行了大量的研究和实验,目前已经实现通过控制技术使燃料电池在适合的状态下运行。显然,这些技术进步保证了燃料电池寿命能够达到预期目标。
最后,燃料电池成本有望继续降低。高成本一直是制约燃料电池商业化应用的关键问题之一。但是,这并不是死命题无法解决。从丰田发展燃料电池汽车的经验来看,基本确定了两条线路来解决这个问题。一是依托材料技术的发展,降低材料成本;二是实现批量化生产,摊薄制造成本。
在材料方面,材料技术大幅度发展使得一辆汽车的催化剂用量降至20~30克,与以往80~100克的用量相比,节省了3倍以上成本。从全球的研发成果来看,催化剂的使用量还在继续降低,实现了材料成本降低的预想。也正是基于此,丰田能够推出量产型燃料电池汽车。
另一方面是批量制造。当前我国的燃料电池汽车数量非常小,所以成本仍然居高不下,所以仍需要一段时间的积累和努力,建议吸收社会力量,通过批量生产使燃料电池成本降下来。
尽管燃料电池技术趋于成熟,但是实现批量生产需要考虑诸多因素。如氢气的制备、氢气的供应等链条都与国家整体的发展情况息息相关。那么,我国目前的储备情况如何?
从氢气的来源来看,我国是全球最大的氢气产出国,美国、德国、日本与我国仍存在一定的差距,电解水制氢技术已经达到国际领先水平,规模达到1000立方米/时,为我国燃料电池汽车发展提供了有力的支撑。
在氢气的供应方面,我国储气瓶的产量在全球也居前位,目前正在攻关70MPa的储氢罐。另外,固体储氢产量也有一定的储备。
在电池性能方面,通过三个五年计划发展,燃料电池用的各种关键材料和零部件,测试性能和实用性能达到了国际水平。
虽然上述准备为我国发展燃料电池汽车打下了坚实的基础,但是在能源战略中,尤其在整机发电能力方面,我国与国外还存在差距。目前国际上已经出现达到几百兆瓦级的整机发电设备,以我国当前的情况来看,这是一项挑战。
如何发展?建议从应用入手,可先解决四个方面的问题。一是电源系统,包括应急电源、备用电源等;二是动力系统,包括车用动力、船用动力等;三是氢能储运,包括可再生能源的储存、运输;最后是分布式供能。
我国也在安排自己的步骤。从燃料电池、氢能储运、氢气制取方面入手,尤其氢气的制取,可通过化石制氢向可再生能源制氢逐步过渡。
与此同时,太阳能和风能的资源与天然气输送管道匹配,可以把太阳能、风能转化成氢气通过管道输送到发达地区。粗略计算,到2020年,如果将20%的风能用来制取氢气,那么每年可生产180亿立方米氢气。
此外,燃料电池的发展需要协同创新,科技界在这方面已经做了许多先导性的工作,需要社会资本、商业模式和产业链企业的共同努力。
(本文根据潘牧在“燃料电池技术在中国的应用与产业化沙龙”现场发言整理,未经本人确认)
