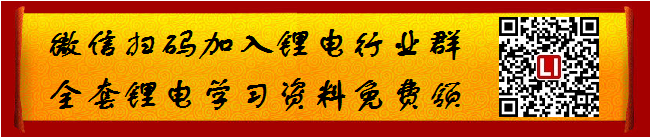
中国动力电池市场不断发酵,其精益求精的要求正倒逼着锂电设备愈来愈向自动化、智能化、柔性化的“三化”特点靠拢。
业内人士指出,由于行业内还没有建立统一的制造和检测标准导致国产动力电池型号规格混乱,大多数电池企业在动力电池叠片、涂布、卷绕和极片焊接等制造环节通常采用半自动甚至是人工肉眼的传统检测方法。
该方法存在检测质量不稳定、检测效率低下、部分缺陷不易识别、漏检率高等多种问题。因此全自动、高精度、智能化的机器视觉在线检测方案成为锂电池检测设备企业解决在线检测顽疾的主流选择。
深圳市天威赛利设备有限公司(下称天威赛利)是一家主要从事锂电池行业的自动组装、自动测试、高精密非标智能设备等自动化的研发及制造为一体的高科技型企业。该企业融合柔性自动化+机器人视觉技术,为业内提出一套一站式智能自动化解决方案。
▲TWSL-350 18650自动贴绝缘纸机
据悉,天威赛利已获得发明专利2项,实用新型专利8项,软件著作5项,同时在申请发明专利6项,实用新型专利21项,软件著作10项。
目前,天威赛利市场主要面向东南亚、美洲等海外。副总经理谭军介绍,“印度是一个依赖进口的国家,其手机电池生产线的自动化设备有约40-50%被我们占领。”并且公司在印度建有自己的驻点办事处,凭借这一业务,今年上半年已拿下3500万的业绩。
与此同时,在国内市场,谭军和他的团队充分运用其在自动化pack与机器人视觉技术多年的经验积累,正逐步打入国产锂电自动化设备高端客户供应链体系。
自动化+视觉如何完美结合应用于锂电池的生产过程中?传统而言,在分选、贴垫片、焊接、打螺丝、检测等系列的锂电池制作中,机器人主要负责装配,而焊接部分则选择人工操作。但锂电池是一个傲娇的东西,其焊接要求要精准、厚度要一致,而人工操作难以完全保证锂电池的一致性。
“组成电池包的每节锂电池都有一个条码,这个条码必须与电阻‘完美匹配’,才能保证电池包的整个电流是一致的。而机器视觉与锂电池生产的操作过程协同,不停地监测、追踪所有的动作,最终汇总成一个巨大的数据库。”谭军说道。
依赖这个数据库,生产者可便捷地查找出“掉队”的锂电池,大大提升生产效率。自动化+视觉两大功能的结合,使天威赛利的设备产品已成功获得德赛电池、飞毛腿、新能动力、迈科、比克等国内锂电企业的青睐。
而笔者去天威赛利拜访的当天,适逢德国客户BMZ来公司验收设备成果。据悉,BMZ是一家在欧洲知名的锂电池PACK德国企业,也是特斯拉的强劲对手。
此次,BMZ向天威赛利采购的产品主要有锂电池分选机和点焊机。谭军透露,“这家公司在国内已经找了10多家设备企业,最终选中了我们。今天他们的技术负责人来验收,光是验收规格书就达80页,而我们的产品说明书都没这么厚。
▲TWSL-700全自动数控点焊机
▲TWSL-1000 18650十档分选机
面对如此“难缠”的客户,天威赛利有哪些成功的秘诀呢?谭军介绍道,“我们非常了解他们的需求,虽然验收规格书有多达80页,但无非强调三点:细节、傻瓜式操作、稳定性。”
比如产品说明书上指出,焊接精度可精确到0.02mm,德国客户会发挥“打破砂锅问到底”的精神,让设备厂以实际数据和技术细节详细解释这一要求实现的可能性。
可以说,明确地了解客户的需求、周到的服务已成为天威赛利决胜市场的第一大法宝。
据谭军透露,在产品方案定案后,一般的生产厂家需要45天的反应周期,但天威赛利仅需一个月,为客户赢得早一步踏上市场“起跑线”的机会。
实现客户“苛刻”要求的技术实力,海外自动化生产经验的丰富积累,再加上谭军机器人集成应用+视觉应用的技术团队的加入,天威赛利打造的自动化+机器视觉方案已成为其最佳的技术武器。
▲部分自动化设备3D图
