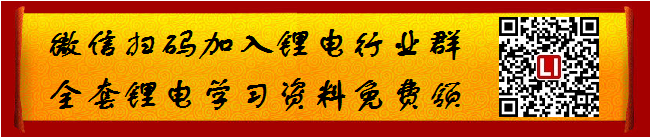
我国动力电池标准化制造问题由来已久,多年来,国内包括政府、车企、电池企业、标准制定机构在内的各方都想牵头制定相关标准。媒体亦不时传出类似“动力电池标准有望统一 发改委牵头近10家车企”的消息。但是迄今为止,动力电池在标准化制造上一直是“雷声大、雨点小”,我国动力电池行业还处在电池路线各不相同、电池型号繁杂、产量分散的较为无序的状态。
近日,据路透社、《日本经济新闻》等媒体报道,日本日产欲出售其在汽车能源供应公司(简称AESC,日产电动车的电池供应商)51%的股份,转而向第三方供应商韩国LG 化学采购电池,以开源节流、降低电池成本。业内人士分析,日产此举将为行业开辟一条“整车厂不把控动力电池”的新路,进一步在国际范围内促进车用动力电池单体乃至成组电池的标准化。
众所周知,纯电动汽车中动力电池模块占整车成本的比例接近50%。如果整车厂商要降低电池成本,在材料和人工成本居高不下的形势下,“标准化制造、规模化制造”是降低电池成本的根本途径。从日产意图出售动力电池业务降低电池成本的举动来看,动力电池的标准化制造问题不仅在国内是个难题,在国外也不例外。那么,动力电池标准化制造为何如此难解,从长远来看究竟有无破解之道呢?
标准化之路“道阻且长”
目前,从国内到国外,新能源汽车厂商大多根据自身生产条件定制动力电池产品,所使用的动力电池在形状、容量、材料上均各不相同,而且大多自己成组。这使得国际范围内的电池标准化制造很难实现,也直接导致电池的制造成本居高不下。
以三款经典的电动汽车日产LEAF、雷诺和特斯拉为例,三家汽车厂商基于产品的定位、电池技术掌握程度等多方面的因素,选择的电池种类、容量、个数和热管理系统就大相径庭(详情参见下图)。特斯拉的优势在于电池管理系统,短板在于单体电池领域的积累不足,因而选择直接从松下购买技术成熟度高、一致性好的18650型电池;而日产从材料解析到单体电池设计再到模组管理都有丰富的经验,因而选择容量较大的层叠式锂离子电池。
日产LEAF、雷诺和特斯拉电池系统参数对比图
国内动力电池制造标准不统一的状况比国外更加严峻。不同电动车企的电池路线、电池规格和测评要求不同,导致动力电池型号繁杂,电池产量分散。业内人士表示,我国动力电池行业内缺乏统一的生产标准,电池缺乏通用性,无法达到标准化、规模化生产,这不仅增加了电池生产成本,也阻碍了动力电池梯次利用的发展。如果国内动力电池产业长期缺失统一标准,未来我国或将引用国外电池制造标准,这意味着整个电池产业链将向国外倾斜,在装备制造、电池成组、电池打包等环节上也要受制于国外。
标准化之难,难在哪里?
据业内人士分析,我国动力电池标准化制造进程之所以如此缓慢,主要因为以下几点原因:
首先,动力电池行业尚未成熟,不同企业在动力电池的选材、设计、连接方式等方面往往不能达成共识,各家对于标准的理解都不一样,很难统一;
其次,从车企的角度来说,对动力电池的选择往往基于对电池技术的掌握程度及产品的定位,动力电池被动地形成了种类、型号等技术参数各不一样;
再次,由于动力电池产业处于初级阶段,各企业尚在探索之中,行业内缺少可以引导标准化形成的巨头。
另外,电池和电动汽车企业均将电池、电池组的设计、工程和控制策略视为核心技术和重要的知识产权。出于保密的考虑,多数企业不愿将自己制造的动力电池参数公之于众,这使得制定行业标准失去了必要的技术参数作为参考。
动力电池制造标准化“路在何方”?
虽然动力电池制造标准化进程比较缓慢,所幸国内多数业内人士已经认识到了标准化制造的重要性,并提出了很多宝贵的建议。
今年年初,中国动力总经理刘宝生曾在公开场合表示,国内不同车企、不同车型的内外部结构设计、模组连接方式、工艺技术各不相同,造成动力电池pack的组装和拆解很难统一。他建议,在电池型号和模组尺寸、功能和接口上推行标准化,有效促进大规模生产,带来更加便捷的维修与替换,同时也带动设备和生产线的标准化。
天津力神电池股份有限公司总裁秦兴才表示,电池行业存在各种不同尺寸、不同形状的包装,电池的型号也都不能统一,不能满足整车企业对动力电池的需求,更不利于电池企业的发展。他认为,应建立电池行业统一标准,像一号、五号及七号电池一样,规范尺寸和标准,推荐给电池行业和整车企业,并联合设备企业共同开发,提高自动化程度。
北汽新能源工程研究院总工程师俞会根则认为,单体电池的型号不统一并不是当前车用动力电池的最大问题,反而是电池组的标准化更加重要。他建议,首先把动力电池模组做成标准化,包括尺寸标准化和DR平台标准化,待模组标准化后再反向规定电芯的规格。
国际范围内,近年来日韩等国均在着力推动动力电池制造标准化的进程。在产学研各界的共同努力下,日韩的动力电池在实现产品标准化、系列化,减少体积、提高功率特性等方面取得了长足的进步。
据业内人士介绍,日韩动力电池产品和国内电池相比显示出的最大特点是灵活的组合,和对各种车辆良好的适用性。同时,日韩动力电池标准化程度的提高降低了电池在生产过程中的控制难度,提高了产品的质量和产量,进一步降低了制造成本。
电池中国网认为,我国动力电池产业虽然发展迅猛,但是从国内来看,动力电池型号过多且尺寸规格不统一,“小而散”的制造方式不利于动力电池产业的健康发展;在国际上也不利于与日韩等国进行竞争。从长远来看,制定合理的模块、规格、序列等标准,形成规模化生产,减少研发与生产成本是国内动力电池保持竞争力的关键。国内动力电池企业、科研机构、政府部门应该联合起来,一方面通过不同的平台,从技术、研发、商业化等多个角度,共同探讨动力电池标准化的相关问题,另一方面应该借鉴国外的成熟经验,共同推动国内动力电池制造标准的制定和实施。
(电池中国网独家稿件,如需转载请注明出处)
