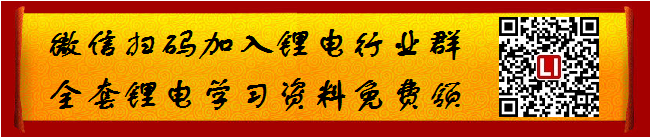
电动汽车正面碰撞试验如下图一所示。GB 11551-2003(乘用车正面碰撞的乘员保护)对壁障的尺寸和安置有明确的规定,要求宽度不小于3m,高度不小于1.5m,壁障前表面应铅垂,其法线应与车辆直线行驶方向成0°夹角,如果有必要,须使用定位装置将壁障固定在地面以限制其移动。
|
|
|
|
|
|
|
|
|
|
|
|
|
|
|
|
|
|
|
|
|
|
|
|
|
|
|
|
|
|
|
|
|
|
|
|
|
|
|
|
|
|
|
|
|
|
|
|
|
|
|
|
|
|
|
|
|
|
|
|
|
|
|
|
| 做好车身结构四点优化,提高低速动力电池正面碰撞安全性"/>|
|
|
|
|
|
|
|
|
| 做好车身结构四点优化,提高低速电动车正面碰撞安全性"/>|
|
|
|
|
|
|
|
|
动力电池正面碰撞安全性"/>|
|
|
|
|
|
|
|
动力电池正面碰撞安全性"/>|
|
|
|
|
|
|
|
电动车正面碰撞安全性"/>|
|
|
| 做好车身结构四点优化,提高低速电动车正面碰撞安全性"/>|
|
动力电池正面碰撞安全性"/>|
|
|
|
|
|
|
|
|
|
动力电池正面碰撞安全性"/>|
|
|
|
|
|
|
|
|
电动车正面碰撞安全性"/>|
|
|
图1正面碰撞试验
一、 着眼于安全角度的车身结构区域划分及设计要求
在车辆的碰撞过程中,整个车身结构从安全角度可划分为三个部分,即前撞吸能部分、乘员舱部分和后撞吸能部分。各部分的设计要求不尽相同,具体要求如下:
(1) 乘员舱部分必须尽可能的保持完整,以保证车内乘员有足够的生存空间;
(2) 碰撞吸能部分要尽可能多地吸收碰撞能量,以降低加速度和碰撞力至合理范围内;
(3) 车身前部吸能构件,在碰撞中产生变形应逐级发生,并使其具有合理的失效模式和压塌顺序,如下图2所示。
图2车身前部结构分级
二、车辆正面碰撞载荷的传递路径设计与优化
汽车前舱在正面碰撞时的主要承载路径有以下三条,如下图3所示:
a. 上前纵梁—A柱—车顶梁;
b. 前端吸能梁(盒)—纵梁—纵梁延伸梁;
c. 副车架—纵梁地板延伸—中央通道、门槛梁。
图3正面碰撞的载荷传递路径示意图
常见的电动汽车动力系统及电池布置,会使得车辆整体重心位置相对燃油车偏下,如图4所示:
图4 电动汽车动力系统及电池布置
针对电动汽车的布置特点,提出的载荷路径传递建议有以下两点:
(1)载荷承载结构布置下移:载荷传递路径的设计思想是通过独特的结构设计来实现对碰撞能量的良好吸收和分散,其主要依据是载荷传递路径的加权高度与整车重心高度相当。当电动汽车因携带动力电池而使重心下移时,其承载结构的布置也需要相应地下移,如图5所示:
图5下移载荷路径
(2)增加载荷传递路径:不同于燃油车的机械传递,电动汽车采用柔性的电线传递能量,使得其空间布置具有一定的灵活性,这也为增加载荷路径创造了有利条件。通过增加载荷传递路径,可以使整个车身结构参与到碰撞吸能中,有利于碰撞能量的迅速吸收和发散,提高承载效率。
三、前舱吸能结构的变形与吸能分析及改善措施
在汽车发生正面碰撞时,车身前部结构的变形形式和能量吸收情况对驾驶员所受的冲击和变形影响很大。在不同的车型当中,虽然主要吸能构件的几何形状、所受约束等情况不尽相同,但普遍地利用薄壁梁作为主要吸能构件,通过薄壁梁的塑性变形来耗散大量的碰撞能量。
如图6的有限元仿真模型所示,在整个碰撞过程中,防撞梁、前围和前底板发生了严重的变形,而两侧纵梁没有发生明显的塑性变形和位移。这说明有大部分碰撞产生的撞击力经纵梁传递到了前围和前底板上。
电动车正面碰撞安全性"/>
图6 前地板、前围、防撞梁、前纵梁(左右)能量吸收曲线
A:底板;B:前围;C:防撞梁;D:前纵梁(左);E:前纵梁(右)
从图6中可以看出,前围和前底板局部发生了明显的塑性变形。而碰撞中,前围板膝盖部位的侵入量大,则有可能影响到乘客腿部的安全。
针对这两处薄弱结构,提出以下优化措施:
(1) 在前地板纵梁前段板及纵梁后端加上两处诱导槽以期在碰撞时间内发生变形吸收更多能量来降低整车的最大加速度。纵梁的变形形式主要分为两种情况:弯曲变形和压溃变形。从能量吸收角度来看,压溃变形要远远好于弯曲变形,它具有更高的能量吸收效率。在车身设计过程中,应尽可能确保纵梁前部出现压溃变形,如因纵梁的结构形式无法全部压溃,也要避免出现大的弯曲变形,以获得较高的能量吸收效率。
(2) 针对前围板侵入量过大的情况,可以从钣金件的厚度与材料方面入手,以减小前围板的侵入量。材料不变,增加前围板的厚度;或者厚度不变,将前围板材料更改为屈服强度与弹性模更大些的新材料。材料的屈服极限大,意味着该材料可以抵抗更大的应力。
四、 电动汽车地板结构特点及优化载荷传递的改进方式
当动力电池安装在地板下方时,为保证一定的离地间隙,电动汽车的坐椅横梁区域与前地板在Z向上必须存在断差,如图7所示。这样,地板从前到后就不是一个完整的部件,产生了一个剪切运动区域,不有利于碰撞载荷的传递。
图7 电动汽车纵梁中心纵向切平面碰撞载荷分布
由电动汽车正面碰撞载荷传递方式可知,其中第2条路径是经中央通道加强梁传递到地板后端。然而,通过路径2的碰撞载荷传递到座椅横梁前端时,由于座椅横梁区域与前地板形成的断差,使得这两部分载荷不能直接传递到地板后端。这就导致这部分碰撞载荷与车辆碰撞时产生的惯性载荷相互作用后在座椅横梁前端产生剪切变形。
针对地板此处的薄弱结构,提出以下优化建议:
(1)在中央通道(座椅横梁)下方增添加强件,并且覆盖住中央通道弯折位置,来减小其在碰撞过程中的变形程度。
(2) 为降低纵梁延长梁根部撞击动力电池的风险,同时进一步缓解中央通道的变形,需要对门槛加强梁与纵梁延长梁搭接件进行优化。比如可以通过增加搭接件与地板的覆盖面积,来增加其抗弯能力。
(3)全新开发地板结构,参考如下:
Smart ED电池箱结构布置在地板座椅下方,地板结构采用“工”字型结构加强方式。如图8所示:
图8 Smart ED电池箱结构布置及地板座椅
Nissan Leaf电池箱的布置及地板结构形式为全新设计的平台,电池包结构由三根纵梁包围进行结构加强,前后设置有缓冲空隙,同时纵梁也增加了载荷的传递路径,能更好的把载荷向后方传递。如图9所示:
图9 Nissan Leaf电池箱的布置及地板结构
以上内容来源于网络,不代表本站立场,如有疑问请联系我们;锂电网(li-b.cn)欢迎投稿。
